随着贸易量的与日俱增,传统依赖人工操作的集装箱装卸模式愈发暴露出诸多棘手问题。一方面,装卸效率的瓶颈日益凸显,人工搬运速度有限,在面对大型货轮动辄数千个集装箱的装卸任务时,往往耗费大量时间,使得船舶在港停留时间延长,不仅增加了港口运营成本,还可能因延误交货期而影响贸易双方的合作信誉。另一方面,人工成本也如 “雪球” 般逐年攀升,吸引和留住熟练的装卸工人愈发困难,企业面临着高昂的人力开支。再者,人工操作过程中的货物安全问题不容忽视,稍有不慎便可能导致货物损坏、丢失,给货主带来经济损失,面对这些严峻挑战,物流行业急需一场 “智能化变革”,而复合机器人的出现,恰如一道曙光,为集装箱运输的困境带来了创新性的解决方案。
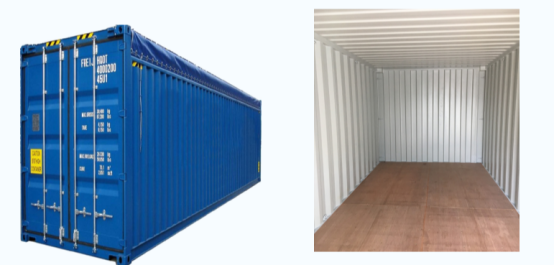
一、复合机器人:智能科技的集大成者
富唯智能精心打造的这款复合机器人,宛如一位拥有 “超能力” 的智能助手,它创新性地融合了机械臂、AGV(自动导引车)和智能控制系统三大核心部件,实现了 1+1+1>3 的卓越效能。
机械臂作为复合机器人的 “巧手”,具备高度的灵活性与精准性。其关节设计精巧,能够在狭小的集装箱空间内自由伸展、旋转,宛如一位技艺精湛的钢琴家在键盘上舞动手指。无论是小巧易碎的精密仪器,还是形状不规则、重量较大的工业零部件,机械臂都能凭借其多样化的抓取工具和先进的力控技术,轻柔且稳固地完成抓取与放置动作,确保货物毫发无损。
AGV 则是复合机器人的 “飞毛腿”,承担着移动与定位的重任。它依靠激光雷达、视觉传感器等先进的导航技术,如同拥有 “火眼金睛” 一般,在集装箱堆场复杂的环境中穿梭自如。即使面对狭窄的通道、频繁往来的其他设备以及各种突发状况,AGV也能迅速规划最优路径,精准停靠在目标位置,误差控制在毫米级别,为后续的装卸作业提供了坚实保障。
而智能控制系统无疑是复合机器人的 “智慧大脑”,负责整体任务的调度与协调。它实时收集机械臂、AGV以及周边环境的信息,运用复杂的算法进行快速分析处理,如同一位经验丰富的指挥官,精准下达指令,确保各个部件紧密配合、协同运作,使整个装卸流程如行云流水般顺畅高效。
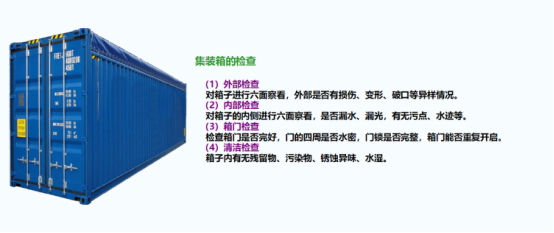
二、严苛测试:见证卓越性能的诞生
1.机械臂操作测试:精准与高效的极致追求
在富唯智能的专业测试场地,一个模拟集装箱环境被精心搭建,这里成为了机械臂展现卓越性能的舞台。测试团队设置了一系列极具挑战性的任务,从微小精致的电子产品零部件,到重达数十公斤、形状不规则的工业铸件,不同尺寸、形状和重量的货物琳琅满目。机械臂在接到指令后,迅速启动,其关节灵活转动,伸展自如,精准地定位到目标货物上方。在抓取精度测试中,面对仅有几毫米公差要求的精密零件,机械臂凭借高精度的传感器和先进的算法,能够以毫米级的误差稳稳抓取,成功率高达 [98%] 以上。例如,在处理一批小型芯片元件时,机械臂需要将其从托盘上逐一抓取并放置到指定的电路板卡槽内,经过多次重复操作,平均误差控制在 ±[0.5] 毫米以内,确保了芯片与卡槽的完美适配,为后续电子产品的组装提供了坚实保障。
而在速度测试环节,机械臂同样表现惊艳。当面对标准尺寸、重量适中的货物时,它能够在短短 [5] 秒内完成抓取、提升、转移和放置的一系列动作,相较于传统人工操作,效率提升了近 [3] 倍。并且,在整个过程中,机械臂始终保持稳定,无论是高速运动还是精细放置,都没有出现丝毫晃动,确保了货物的安全。即使在长时间、高强度的连续作业下,机械臂的稳定性依然可靠,为集装箱装卸作业的高效、持续进行奠定了坚实基础。
2.AGV 移动与定位测试:穿梭自如的智能领航
集装箱堆场,向来是一个复杂多变的作业环境,车辆穿梭、设备林立、货物堆放高低不一,犹如一座巨大的 “迷宫”。然而,富唯智能的 AGV 却在这里如鱼得水,展现出非凡的自主导航与避障能力。测试人员设定了多条复杂的行驶路径,既有狭窄蜿蜒、仅容一辆车通过的通道,又有需要连续转弯、掉头的局促区域。AGV 凭借其搭载的激光雷达、视觉摄像头等多种高精度传感器,实时感知周围环境,迅速构建出精确的地图。在行驶过程中,它能够提前预判障碍物的位置、速度和移动方向,以每秒 [2] 米的速度灵活穿梭,精准避障,从未发生过碰撞事故。
在定位精度测试方面,AGV 更是展现出了令人惊叹的 “绝技”。当接到停靠指令后,它能迅速调整姿态,准确无误地停靠在指定位置,误差始终控制在 ±[3] 毫米以内,远远优于行业 ±[10] 毫米的平均标准。这意味着,AGV 能够为机械臂提供极其精准的作业起始点,确保货物的装卸操作精准高效。例如,在与大型集装箱起重机协同作业时,AGV 需要在起重机下方狭小的区域内精准定位,以承接从集装箱内吊出的货物。多次测试结果表明,AGV 每次都能与起重机的吊运节奏完美配合,高效、安全地完成货物转运任务,充分验证了其在实际工作环境中的高度稳定性与可靠性。
3.整体系统联动测试:协同无间的高效合奏
将机械臂与 AGV 进行联动,模拟真实的集装箱装卸、搬运、码垛全流程,无疑是对复合机器人系统的终极考验。测试团队精心设计了多个复杂的任务场景,涵盖了不同货物类型、装卸顺序以及紧迫的节拍要求。
在一个模拟港口高峰期作业的场景中,多台复合机器人同时接到任务,需要在短时间内完成一艘大型货轮上数百个集装箱的卸载、搬运与分类码垛。机械臂与 AGV 紧密配合,AGV 根据智能控制系统的调度,迅速行驶至集装箱下方,精准定位后,机械臂立即启动,以高效的抓取速度将货物稳稳取出,放置在 AGV 承载台上。随后,AGV 沿着最优路径快速驶向仓库,途中灵活避开其他忙碌的设备与临时出现的障碍物,抵达仓库后,机械臂再次精准操作,将货物按照预设的分类规则整齐码放。整个过程如同一曲精心编排的交响乐,各个环节紧密衔接,节奏明快。经统计,在这一高强度作业场景下,复合机器人系统相较于传统人工装卸团队,作业效率提升了 [4] 倍以上,且货物损坏率从原本的 [2]% 大幅降低至 [0.1]% 以下,充分彰显了其卓越的协同能力与高效性,为未来集装箱码头的智能化运营描绘了一幅宏伟蓝图。
AGV移动与定位测试:在集装箱堆场环境中,测试AGV的自主导航、避障、定位精度等功能。通过设定不同的路径和障碍物,验证AGV在实际工作环境中的稳定性和可靠性。
整体系统联动测试:将机械臂与AGV进行联动,模拟实际的集装箱装卸、搬运、码垛流程。通过设定不同的任务场景和节拍要求,评估整体系统的协同能力和效率。
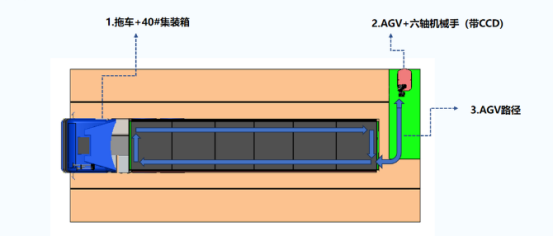
经过多轮测试,复合机器人在集装箱操作中的表现良好。机械臂能够精准地抓取和放置货物,AGV能够稳定地移动和定位,整体系统联动顺畅,能够高效地完成集装箱的装卸和搬运任务。
本次复合机器人集装箱测试项目成功验证了机器人在集装箱操作中的可行性和优势,为后续的大规模应用奠定了基础。