在新一轮科技革命和产业变革的浪潮中,“智能制造” 已成为工业领域的核心议题,深刻影响着全球制造业的发展走向。那么,究竟什么是智能制造?它是新一代信息技术与先进制造技术深度融合的产物,以数字化、网络化、智能化为核心特征,贯穿于产品设计、生产规划、生产执行、售后服务等产品全生命周期,构建起具有自感知、自学习、自决策、自执行、自适应功能的先进生产模式 ,重塑着制造业的生态格局。
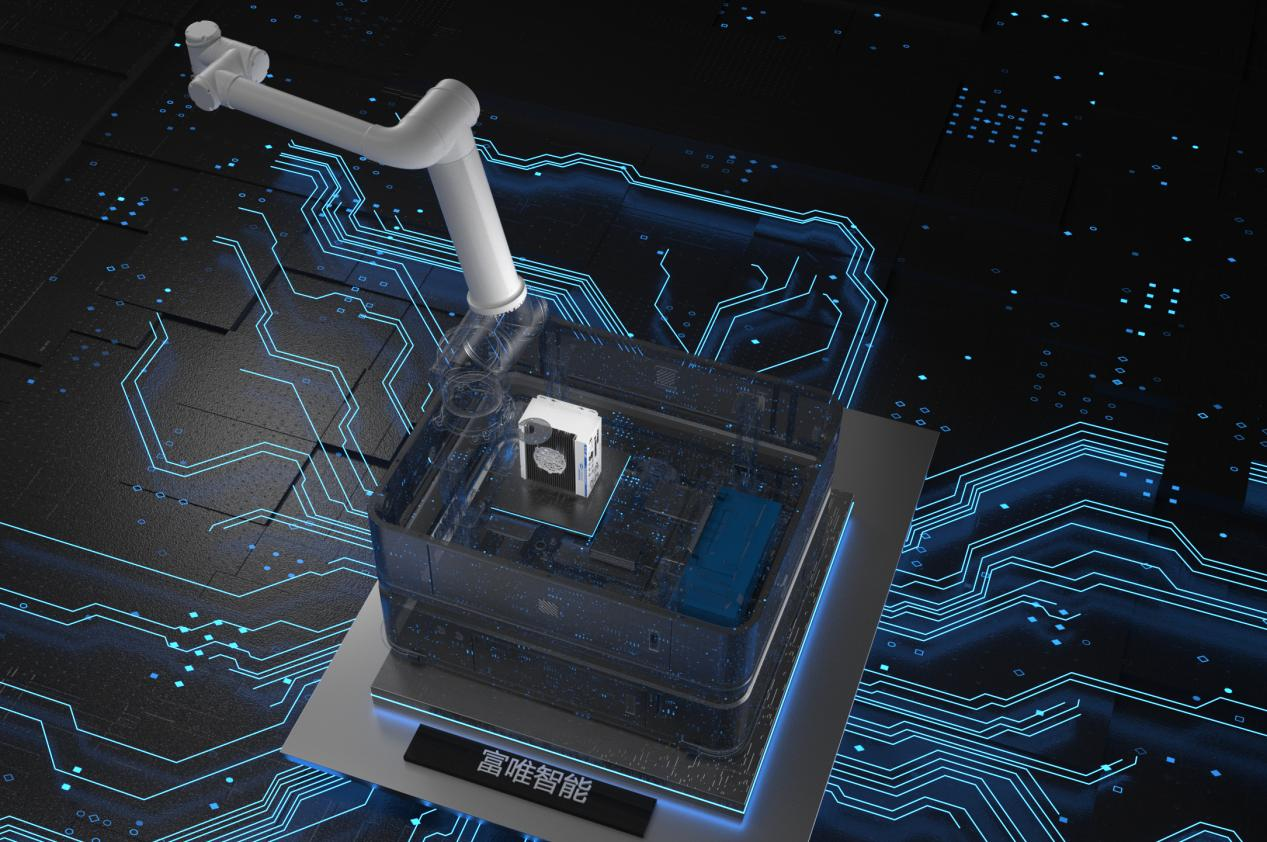
智能制造依托于一系列前沿技术的协同支撑。从工业互联网来看,它遵循 IEEE 802.11、OPC UA 等标准协议,通过有线、无线等多种网络架构,构建起全方位的互联互通体系。在工厂内部,基于 TSN(时间敏感网络)技术实现设备之间的高精度时间同步通信,确保数据实时、准确传输,为生产过程的实时监控与优化提供了坚实基础。借助工业互联网平台,如西门子的 MindSphere、GE 的 Predix 等,实现设备数据的汇聚、分析与应用,基于大数据分析技术对生产数据进行深度挖掘,利用聚类分析、关联规则挖掘等算法,企业能够精准洞察生产过程中的潜在问题,实现预防性维护,降低设备故障率。
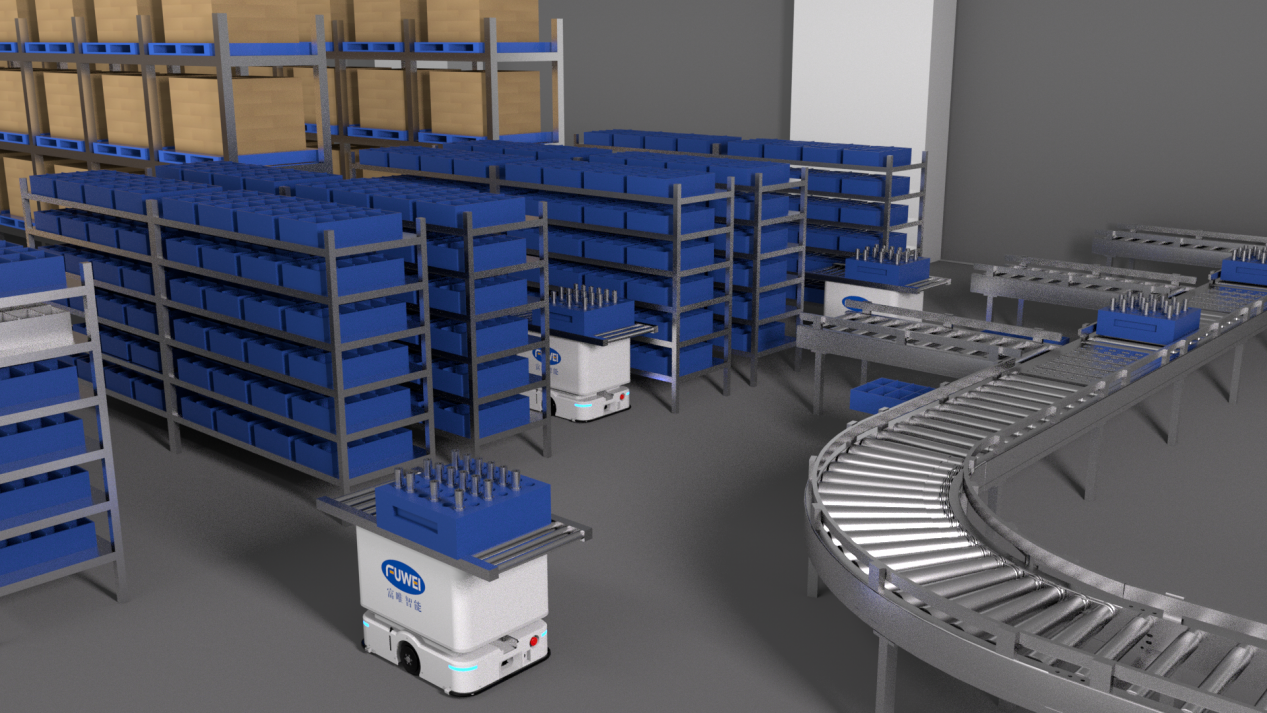
在人工智能领域,机器学习算法在智能制造中发挥着关键作用。以深度学习中的卷积神经网络(CNN)为例,在工业图像识别任务中,通过构建多层卷积层、池化层和全连接层,对大量工业产品图像进行有监督学习,自动提取图像特征,实现对产品表面缺陷、尺寸精度等的高精度检测,检测准确率可达 99% 以上。强化学习算法则应用于机器人路径规划与任务调度,机器人在与环境的不断交互中,根据奖励反馈机制,利用 Q-learning、深度 Q 网络(DQN)等算法,逐步学习到最优策略,实现高效、灵活的作业。
数字孪生技术基于 ISO 18435 等国际标准,通过多物理场建模、数据融合等技术,构建与物理实体高度映射的虚拟模型。在航空发动机制造中,利用有限元分析、计算流体力学等方法对发动机的机械结构、热性能、流体动力学等进行多物理场耦合建模,实时采集发动机运行数据,通过数据融合技术更新虚拟模型,实现对发动机全生命周期的实时监控与优化,可将研发周期缩短 30% 以上。
边缘计算在智能制造中的应用,遵循 IEC 62443 等工业信息安全标准,通过在设备端或网络边缘部署计算节点,利用容器化技术实现应用的轻量化部署与隔离,对传感器采集的海量数据进行实时处理。例如在智能工厂中,边缘计算节点可在毫秒级时间内完成对设备运行状态数据的分析,当检测到异常时,立即发出控制指令,保障生产线的稳定运行。
在工业制造上下料环节,智能制造优势显著。3D 视觉技术采用结构光、激光三角测量等原理,结合张氏标定法等高精度标定技术,实现对物料的高精度三维重建与位姿估计。搬运机器人基于机器人运动学 D-H 参数模型,通过逆运动学求解实现精确的轨迹规划,配合先进的伺服控制系统,可实现重复定位精度 ±0.05mm 以内的物料搬运。
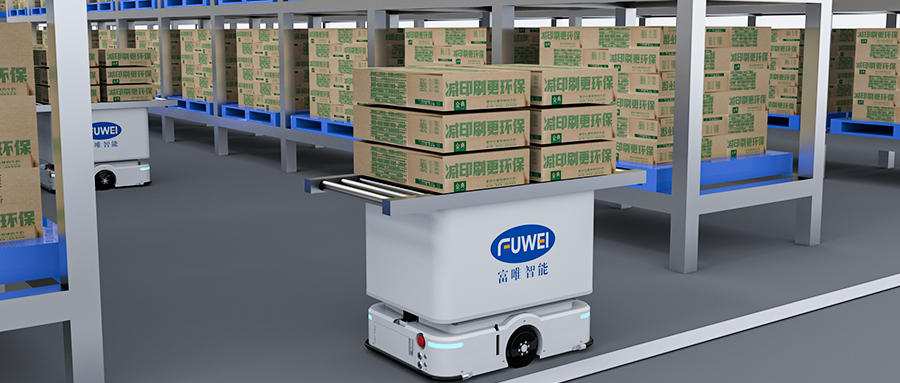
制造执行系统(MES)依据 ISA-95 标准,通过实时数据采集与分析,利用排程算法对上下料任务进行智能调度。当检测到某加工工位物料不足时,MES 系统基于线性规划、遗传算法等优化算法,在数秒内完成搬运机器人的任务分配与路径规划,确保生产线的连续运行。
展望未来,随着 5G、人工智能、区块链等技术的持续创新与融合应用,智能制造将朝着自主决策、深度协同、可信安全的方向加速发展,在全球制造业变革中发挥更为关键的引领作用。