项目背景
在当今制造业自动化升级的趋势下,本次项目聚焦于复合机器人 CNC 自动上下料领域。旨在通过先进的自动化技术,实现对多台 CNC 机床的高效上料和下料操作。在生产过程中,CNC 机床内加工的产品先由操作人员整理放置于小托盘内。这些装有产品的小托盘需要通过自动化方式在 CNC 加工中心与其他区域之间进行流转,而 CNC 加工中心有特定的放置位置参数,其高度为 1000mm,深度为 400mm,并且每台机床的加工时间在 15 - 20min 之间。整个项目计划使用 1 台复合机器人完成对 8 台 CNC 机床的上下料工作,这对来料和下料方式的规划提出了较高要求。
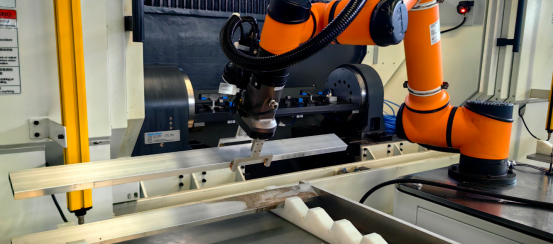
项目难点
1、上下料流程复杂
需要协调操作人员、转运机器人、复合机器人以及输送线等多个环节,确保待加工产品从整理到上料,以及加工成品从下料到人工理料区的流程顺畅且准确。
2、定位与抓取精度要求高
复合机器人需要通过 3D 视觉和机器人夹爪对小托盘进行准确的取出和放置操作,尤其是在 CNC 机床内部有限的空间和特定的位置条件下,要保证高精度的定位和抓取,避免碰撞等问题影响加工效率和产品质量。
3、多台机床协调作业
1 台复合机器人要服务 8 台 CNC 机床,需要合理安排其在各机床之间的移动顺序和时间,保证各机床的上下料需求都能及时响应,同时避免机器人在移动过程中的冲突和等待时间过长的问题。
4、来料和下料方式规划
要考虑待加工产品和加工成品的来料和下料方式,确保物料在不同环节之间的有效转接,避免物料堆积或供应不足的情况。
解决方案
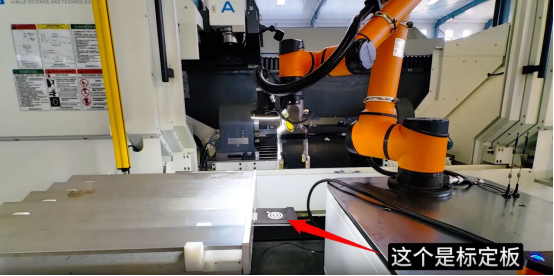
1、来料流程
操作人员将托盘上的待加工产品放置到输送线大托盘的小托盘上。随后,转运机器人移动到输送线接驳位,将待加工的大料盘接驳到自身。接着,转运机器人前往对应的 CNC 机床旁边的上料料架接驳位,并将大料盘送入上料料架。
2、上料流程
复合机器人移动到 CNC 机床上料位,利用 3D 视觉 + 机器人夹爪的先进技术,从已就位的上料料架上准确取出小料盘,并将其放入 CNC 机床内,然后退出,为机床加工做好准备。
3、下料流程
当 CNC 机床加工完成后,复合机器人移动到 CNC 机床下料位,再次借助 3D 视觉 + 机器人夹爪,将机床内加工完成的小料盘取出,放置到 CNC 机床旁边下料料盘的大托盘上,之后退出。
4、成品转运流程
当下料料盘满料后,转运机器人移动到 CNC 下料料盘接驳位,通过输送线将满料的加工成品大料盘接驳到自身,然后将其转运至人工理料区,完成整个加工成品的下料流程。
核心价值
1、提高生产效率
通过自动化的上下料流程,减少了人工操作时间和错误,并且复合机器人和转运机器人的协同作业可以快速响应多台 CNC 机床的需求,大大缩短了加工周期,提高了整体生产效率。
2、提升产品质量
复合机器人的 3D 视觉和高精度夹爪技术保证了上下料过程中的准确性和稳定性,减少了因人为因素或操作不当导致的产品损坏,从而提升了产品质量。
3、降低人力成本
原本需要大量人力参与的上下料工作,现在大部分由自动化设备完成,减少了对人工的依赖,降低了人力成本,同时也避免了因人员疲劳等因素对生产的影响。
4、增强生产灵活性
该解决方案可以根据实际生产需求,灵活调整复合机器人的工作路径和转运机器人的接驳顺序,适应不同的加工任务和产品类型,为企业的多样化生产提供了有力支持。